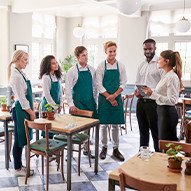
Strategies for Small Business Owners to Leverage Before the Festive Season
Marketing and Customer Relations
This guide will delve into some practical tips, effective marketing techniques and essential strategies to help you maximize your sales and ensure a successful holiday season.
Read More